Production Methods
.png)
During the project, I learned mass production methods by creating moulds of an existing kettle design and replicating identical new pieces.
Process
The different parts were manually sketched out and dimensions of each part was roughly noted. Caliper was used during the elaborate process. The rough sketches were used to create digital technical sketches.
Dimensions Study

Technical Drawing
Actual scale
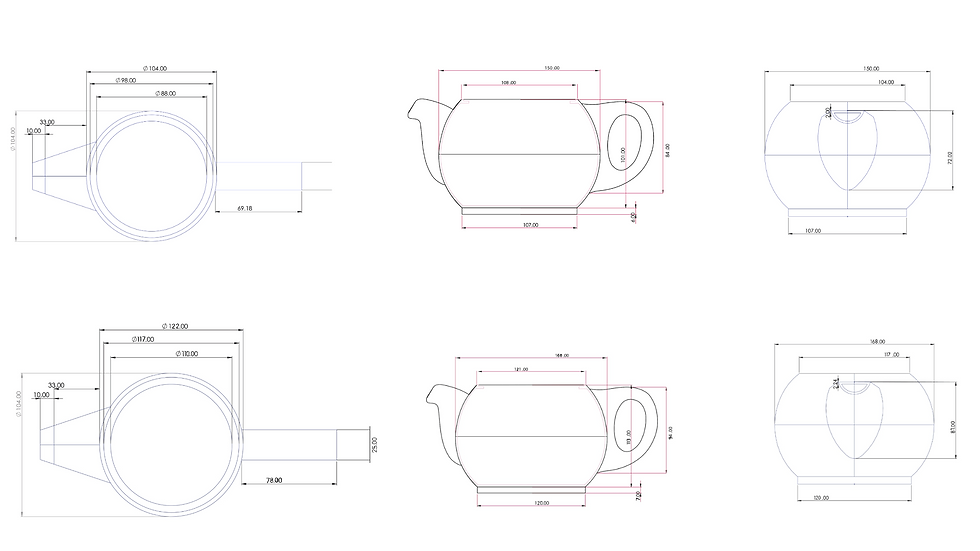
12% Increase
Stoneware shrinks by 12% after bisque firing which is not the same before firing. Hence, product must be made keeping in mind the 12% margin and increasing the dimensions accordingly.
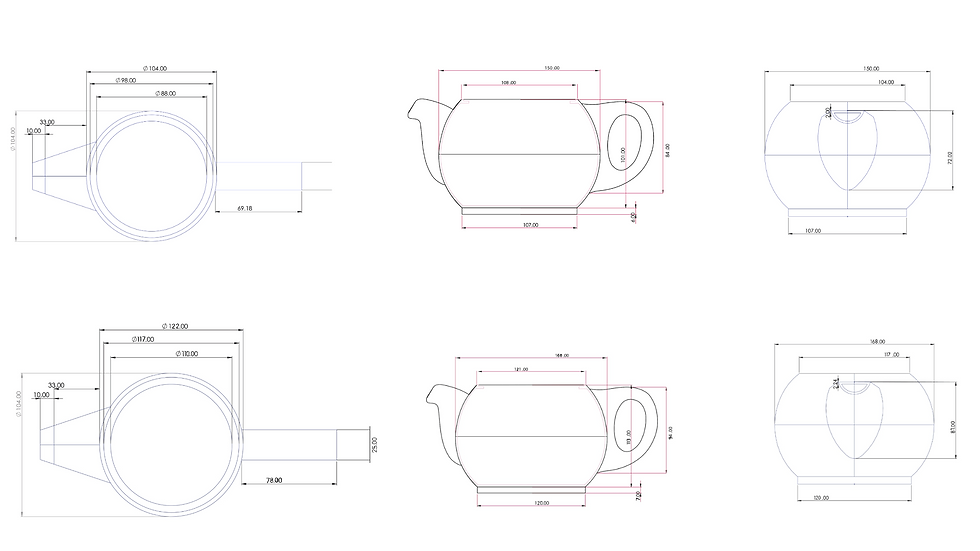
Profile Making Steps

Model Making
Body
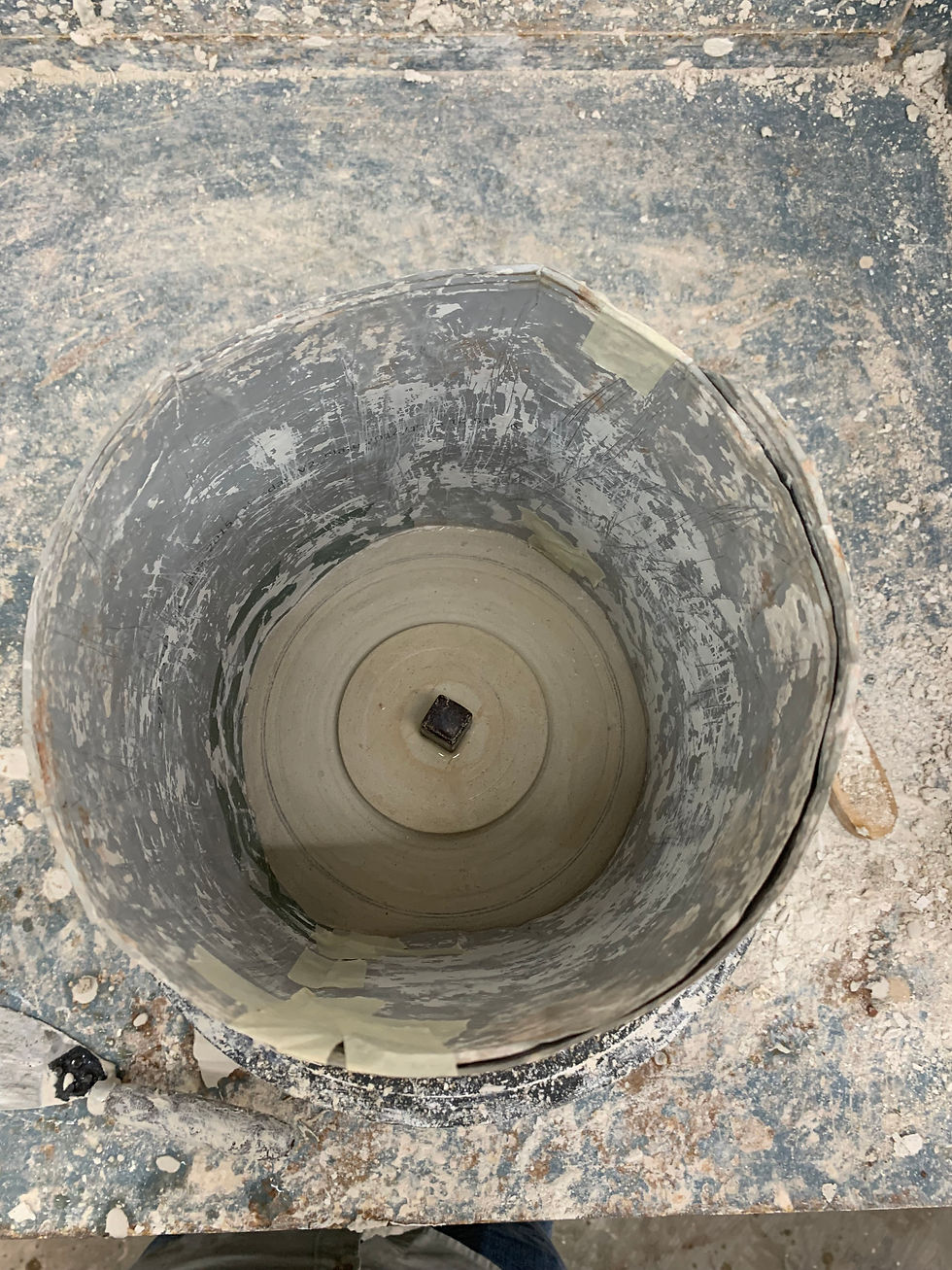
A metal sheet is used to make a cylinder above the plaster wheel where the POP block will be casted

Folded cylinder is sealed with the plaster wheel with thick POP to stop the liquid POP from coming out while pouring.

Once the prepared cylinder mould is dried, liquid POP (fairly fluid consistency)is prepared in a good amount and poured inside the cylinder mould through the sieve.
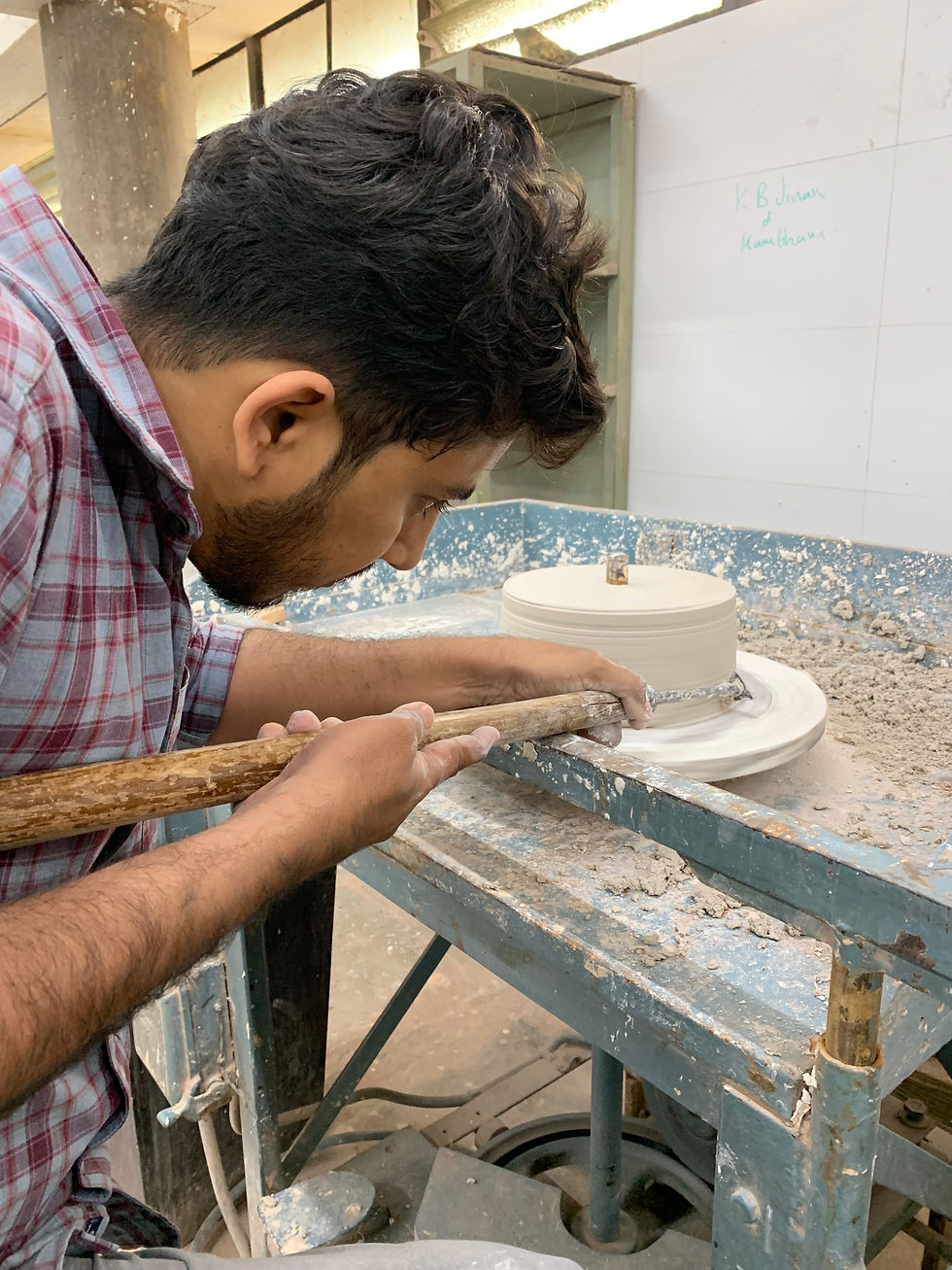
POP block is then carved out using triangular carving tool. First carving the the basic height and width of the model and then giving the details as per profile.

Model is cross checked with the drawing for final touches
Spout

Casting POP block for the spout
Spout model after carving the block
Stages of carving the spout using hack saw blade and sand paper
.png)
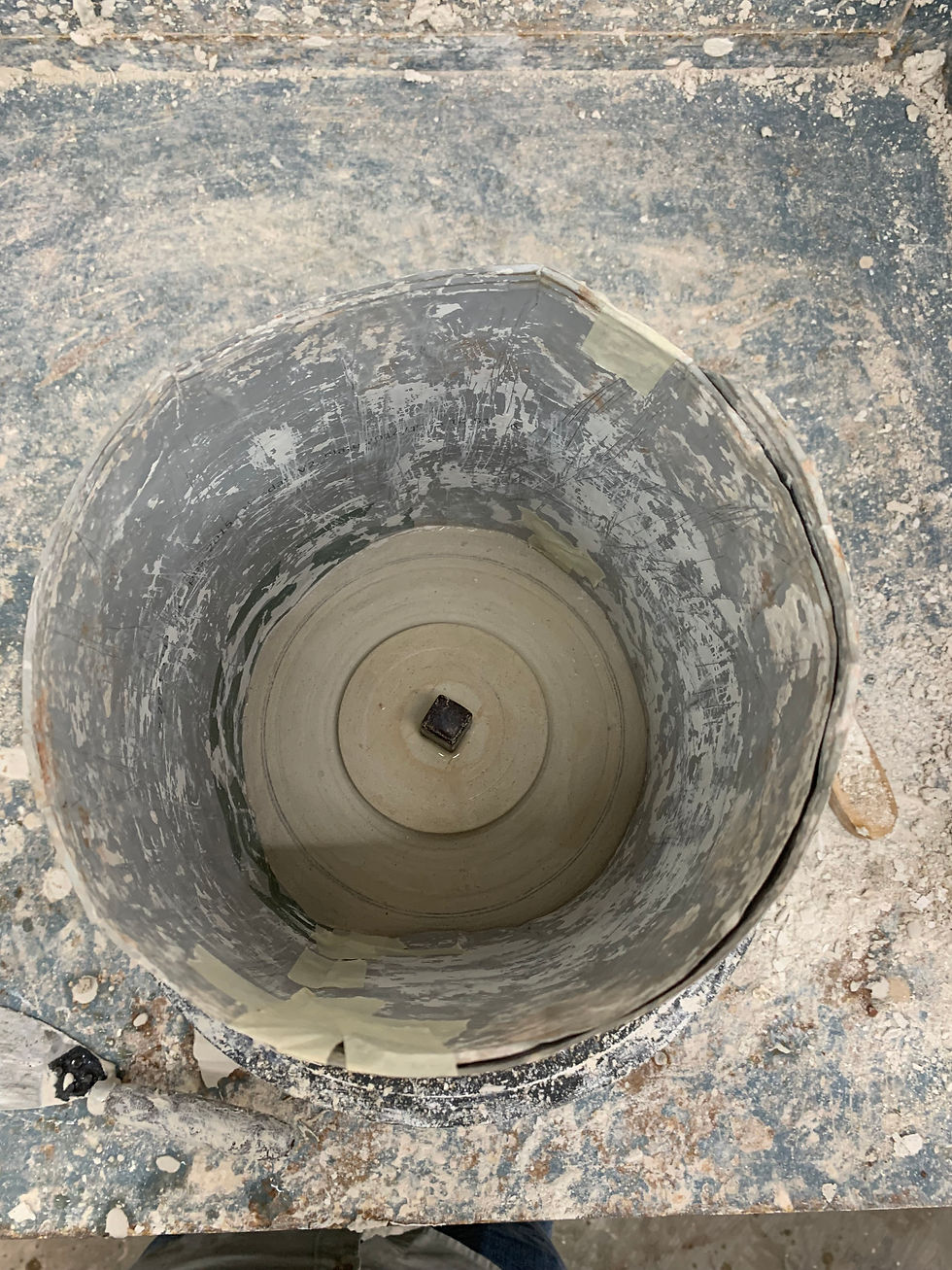



Handle
Rim
Handles can be slip casted as well as press casted. Strength is more when it is press casted as it remains solid.
Rim of the model is casted first with a V groove for locking with other parts. Soap solution is applied on the rim and outer areas. Then, a thick paper is used to cover the rim and POP is poured inside at 1.5 inches above the rim.
A four piece mould is the final outcome of the process. One is the rim which is made earlier, two halves are obtained from the main body and fourth is the top created for pouring slip.
Mould making
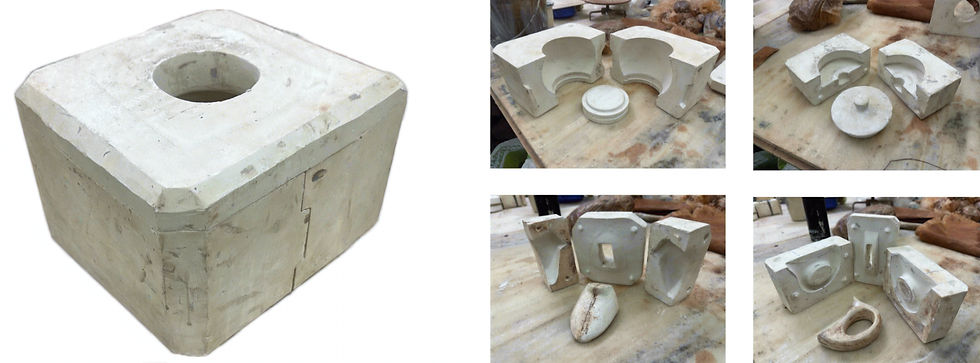
Bisc Fire
Stoneware slip cast
Glaze
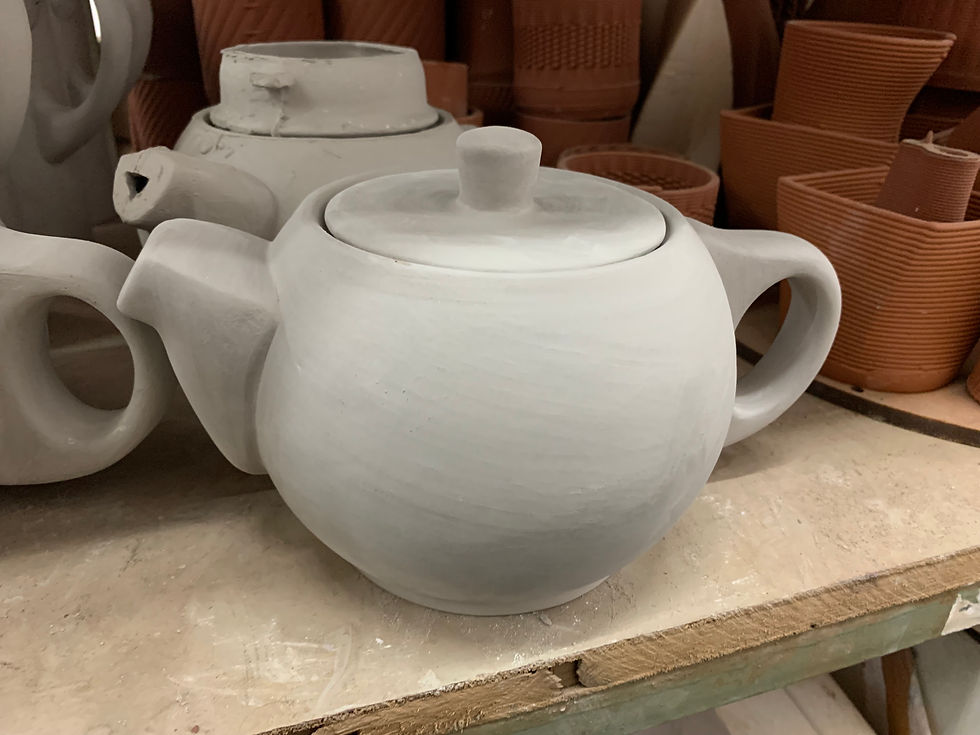

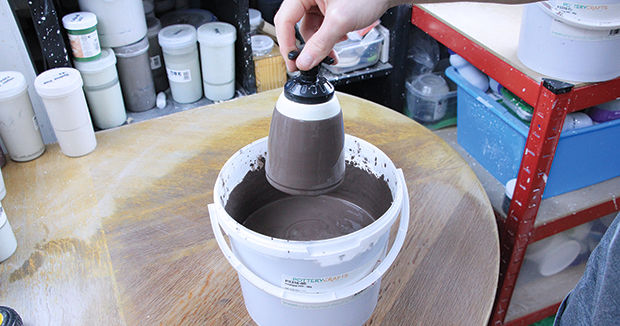
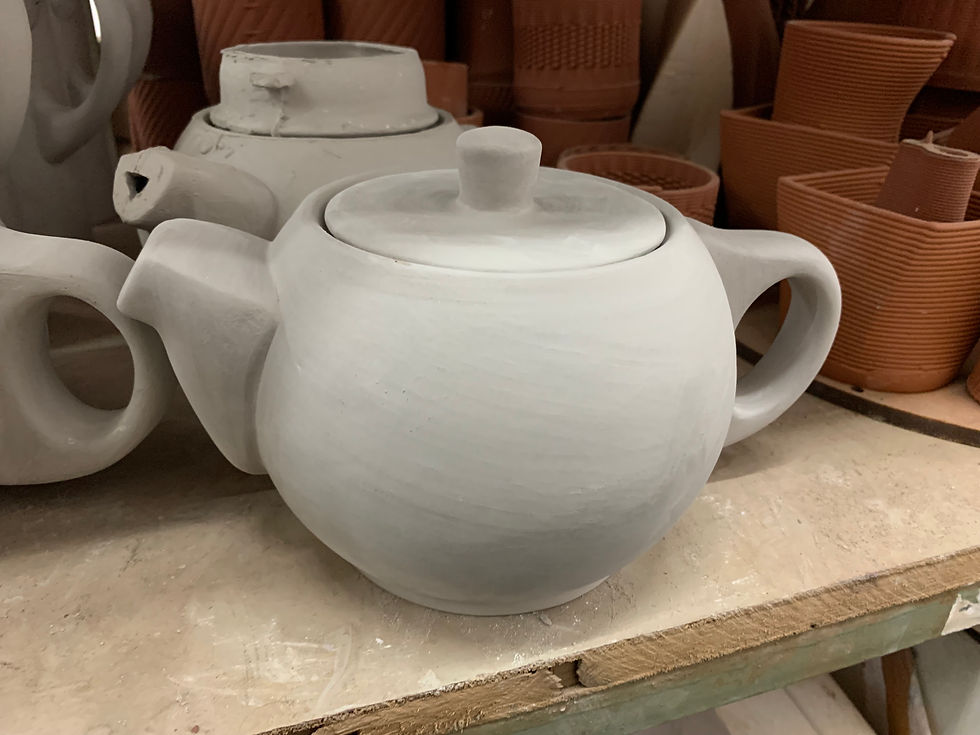
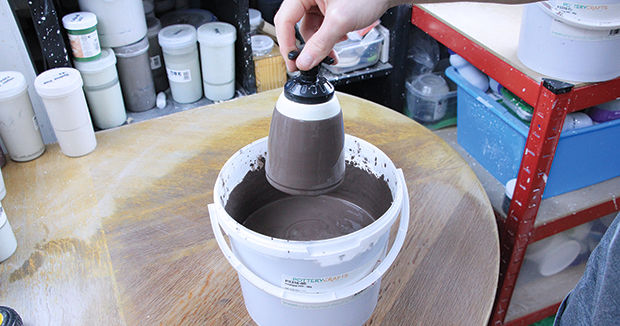
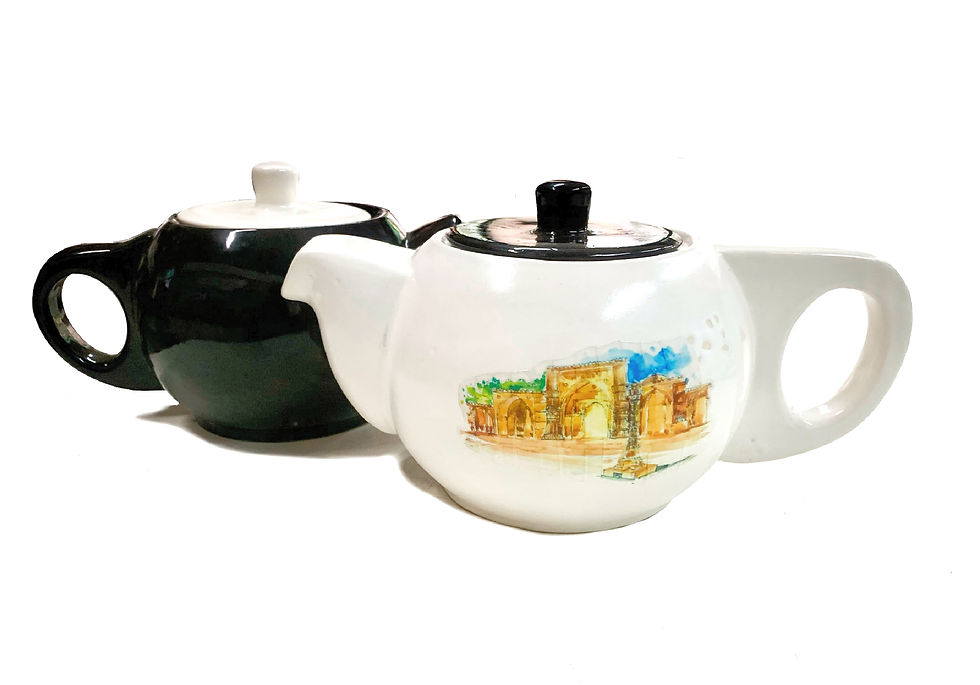